Quality and certification
COMMITMENT AND POLICY
For Safety, Quality and the Environment, INVEHO undertakes to deploy a single strategy across each of its sites, in line with STREEM’s commitments, to ensure that all stakeholders are safe, deliver customer satisfaction, and reduce our carbon footprint.
INTERNAL TRAINING
Bridge crane operator accreditation
Trainings delivered are based on CNAM recommendation R484. The goal is to provide the theoretical and practical knowledge required to operate bridge cranes, learn safe slinging rules, and deliver the operating authorization > the goal is the carriage of heavy loads in the workshop.
Forklift truck operator (R489 category 3) and heavy plant machinery operator (R482 category F) accreditations
These training courses are based on recommendation R489 category 3 for forklifts with a design capacity of < 6,000kg, and recommendation R482 category F for worksite machinery.
The goal of these trainings is to prevent risks and optimise safety on plants. It also allows to meet the training obligation with the aim of delivering an operating authorization > handling of wheelsets in the facility, loading and unloading of heavy equipment are the target.
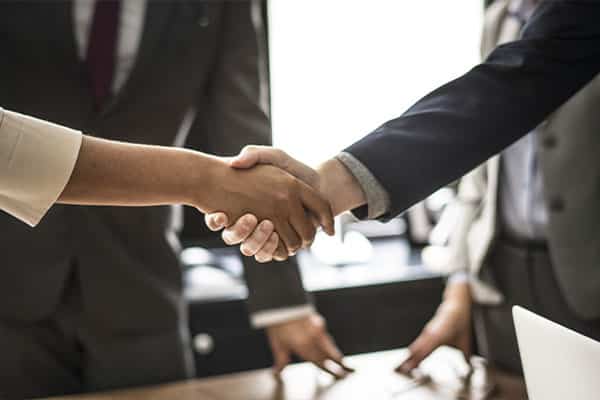